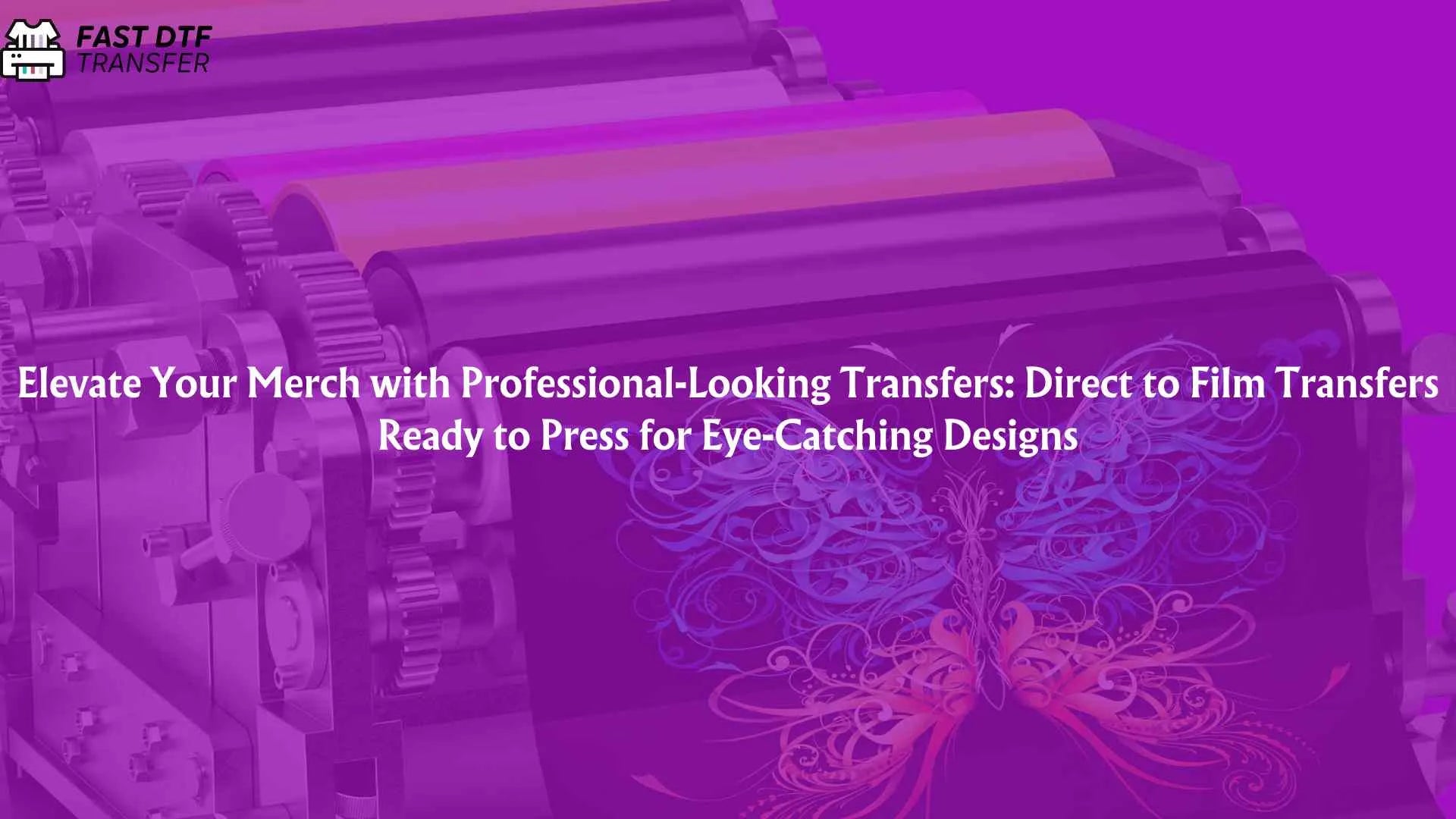
Elevate Your Merch with Professional-Looking Transfers: Direct to Film Transfers Ready to Press for Eye-Catching Designs
Why DTF Transfers are a Game-Changer for Merch Design
Revolutionizing Merch Design: The Rise of DTF Transfers
The world of merchandise design has undergone a significant transformation with the advent of Direct-to-Film (DTF) transfers. These innovative transfers offer a plethora of advantages that are revolutionizing the way custom apparel is created. While traditional methods like silkscreen and heat transfer have their merits, DTF transfers stand out as a clear frontrunner for several reasons.
Enhanced Versatility and Detail
DTF transfers excel in their ability to reproduce intricate designs with exceptional clarity and vibrancy. This is attributed to their unique printing process that utilizes a special ink that adheres directly to the film. This not only preserves delicate details but also allows for a wider range of designs, including gradients, halftones, and even photographic images.
Faster Production and Cost-Effectiveness
DTF transfers offer a significant boost in production speed compared to traditional methods. The absence of lengthy curing processes leads to faster turnaround times, enabling businesses to fulfill orders more efficiently. Additionally, DTF transfers are relatively inexpensive to produce, making them an attractive option for businesses of all sizes.
Ready-to-Press Convenience
DTF transfers are pre-coated with a release agent, eliminating the need for separate coating steps. This straightforward approach simplifies the production process and reduces the risk of errors. Moreover, DTF transfers are ready-to-press, allowing businesses to skip the drying process and directly apply them to the desired garments.
Eco-Friendly and Sustainable
Environmental consciousness is at the forefront of today's business practices. DTF transfers align with this eco-conscious trend, utilizing water-based inks that are less harmful to the environment. This commitment to sustainability further enhances the appeal of DTF transfers among discerning customers and businesses.
The DTF Process: From Digital to Physical
Direct to Film (DTF) printing is a revolutionary technique for transferring digital designs onto a variety of substrates, including clothing, bags, hats, and more. This process offers a number of advantages over traditional methods like screen printing and heat transfer, including:
- Vivid colors and sharp details: DTF transfers produce high-quality images with vibrant colors and precise details, making them ideal for intricate designs and text.
- Durability: DTF transfers are incredibly durable, resisting fading, cracking, and peeling. They can withstand repeated washing and drying without compromising their quality.
- Versatility: DTF transfers can be applied to a wide range of materials, including both light and dark fabrics, as well as rigid surfaces like plastics and wood.
- Ease of use: DTF printing is relatively simple to learn and can be done at home with the right equipment.
Benefits of Using Direct to Film Transfers
Direct to film transfers ready to press offer several benefits for businesses and individuals alike:
- Quick turnaround times: DTF transfers can be printed and applied quickly, making them ideal for short-run projects and on-demand printing.
- Low cost per unit: DTF printing is an affordable option for high-volume printing, making it a cost-effective choice for mass production.
- Customized designs: DTF transfers can be customized with any design imaginable, making them perfect for personalized products or promotional campaigns.
- No minimum order requirements: DTF printing does not require large minimum order quantities, making it accessible to small businesses and individuals.
Key Considerations to Maximize Transfer Quality
Achieving flawless transfers with direct to film (DTF) printing requires meticulous attention to detail and the right approach. Here are some key considerations to maximize transfer quality and produce stunning results:
High-Quality Printer Ink:
Utilize high-quality DTF ink specifically designed for this printing process. Ensure the ink is compatible with your printer and the specific substrate you'll be applying the transfer to.
Proper Pre-Treatment:
Prior to printing, thoroughly pre-treat the substrate to enhance ink adhesion and prevent cracking or peeling. Use a recommended pre-treatment solution or apply a thin layer of adhesive to the garment.
Accurate Template Creation:
Carefully create a template that aligns perfectly with the garment's dimensions. Avoid using low-quality templates or images that may result in distorted or pixelated designs.
Consistent Temperature and Pressure:
Maintain consistent temperature and pressure during the heat press stage. Incorrect settings can lead to incomplete transfer, color bleeding, or bubbling.
Proper Air Drying:
Allow the transfer to air dry fully before removing it from the garment. Haste can cause the design to tear or lift off.
Optimal Pressing Duration:
Follow the manufacturer's recommended pressing duration for the specific DTF ink and substrate. Excessive or insufficient pressing can affect transfer quality.
High-Quality Sublimation Transfer Paper:
Use high-quality sublimation transfer paper specifically designed for DTF printing. This paper ensures smooth ink transfer and vibrant color reproduction.
Heat Press Techniques for Seamless Transfers
Direct-to-film (DTF) printing offers a versatile and cost-effective way to create durable, high-quality transfers onto a variety of substrates. However, achieving seamless transfers requires careful attention to heat press techniques.
Proper Preheating:
Before pressing, preheat the heat press to the recommended temperature for the specific DTF ink and substrate. This ensures even heat distribution and prevents scorching or warping.
Even Pressure Distribution:
Apply consistent pressure throughout the pressing process to ensure complete transfer of the ink. Use a pressure gauge to monitor pressure and maintain a balanced distribution.
Accurate Positioning:
Align the transfer precisely on the substrate, ensuring it is properly centered and free of wrinkles or folds. Misalignment can result in distorted or incomplete transfers.
Gradual Ramping Up:
Start the heat press at a low temperature and gradually increase to the desired setting. This allows the substrate to warm evenly and prevents thermal shock, which can damage the transfer.
Full Coverage:
Press the heat press for the recommended duration, ensuring the entire transfer is completely covered. Avoid pressing too briefly or excessively, as this can affect transfer quality.
Gradual Cooling:
After pressing, gradually lower the heat press temperature and allow the transfer to cool completely before peeling it off. This prevents cracking or peeling of the ink.
Proper Peeling Technique:
When peeling the transfer, start from the edges and gently lift it away from the substrate. Avoid pulling or tearing the transfer, as this can damage the ink.
In conclusion
Direct to film (DTF) transfers ready to press offer a revolutionary approach to merchandise design, combining exceptional versatility, durability, and affordability with a streamlined production process. Whether you're a small business owner creating personalized apparel or a seasoned printing professional seeking efficient high-volume solutions, DTF transfers are the ideal choice for elevating your merch game and crafting eye-catching designs that captivate customers and stand the test of time.
Leave a comment
This site is protected by hCaptcha and the hCaptcha Privacy Policy and Terms of Service apply.